Process Mapping: Understand and Improve Processes
«A bad process will beat a good person every time» - W. Edwards Deming
Are Your Processes Optimized for Success?
How well do your processes flow? Are your activities value-adding? Is the process performed the same way every time?
To improve a process, we first need to understand it. Process mapping helps visualize and analyze processes as they actually work, making it an essential tool for process improvement.
Benefits of Process Mapping
Process maps visually illustrate how activities connect to achieve a result. They are used for formal documentation, process improvement, and designing new processes.
Commonly, symbols and color codes are used to clarify activity types. Various process maps serve different purposes, but they all help individuals understand their roles and interactions within the bigger picture.
An inefficient process will yield poor results, no matter how skilled the people executing it are.
Why Use Process Mapping?
Process mapping provides insight into workflow, highlights improvements, and clarifies roles.
Benefits:
- Provides a clear overview of the entire process
- Helps team members understand their role
- Useful for training new employees
- Identifies key measurement points for improvement
- Reveals inefficiencies and bottlenecks
- Supports data collection and root cause analysis

Join Our Value Stream Mapping Course
Learn how to map and optimize processes using various process mapping techniques. Sign up for our Value Stream Mapping course today!
How to Perform Process Mapping
- Determine the process to be mapped
- Define the process start and end points
- Identify the main activities within the process
- Include decision points and alternative paths
- Incorporate inspections and quality controls
- Highlight areas for improvement
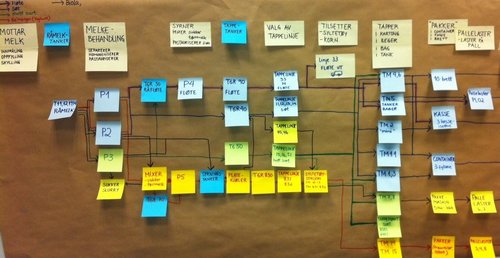
To ensure accuracy, observe the actual process ("Go to Gemba") and involve those performing the tasks. Ask questions and verify the workflow.
«Flow charts should be as simple as possible, but not simpler» - Albert Einstein
Ask Questions to Improve the Process
- What is the purpose of this process?
- How do we ensure we achieve the desired outcome?
- What factors influence the process results?
- Are inspections or quality controls conducted?
- What happens if an inspection fails?
- Are there any bottlenecks?
- Are any activities performed more than once?

Different Types of Process Maps
There are many types of process maps, each suited for different purposes. Here are some examples:
- SIPOC (Supplier - Input - Process - Output - Customer): Provides an overview of the process and helps prioritize improvements.
- Spaghetti Diagram: Visualizes movement and transportation of people, goods, and information.
- Value Stream Mapping: Analyzes process steps and key data related to flow and value-adding activities.
- Swimlane Diagram: Shows process steps and who is responsible for each stage.
- Process Variable Map: Helps identify factors that affect quality and performance.
Which process map is best suited for your needs?
Lean Tech Facilitates Process Mapping
We help businesses implement effective process mapping. Contact us for more information!